Thanks to The Future Group we currently have this sweet Xsens MTi 30 AHRS at our office. We wanted to use this to log vibrations on our home made 3D printer desk while printing. We also wanted to apply damping in a couple of different ways to see if we got any different restults.
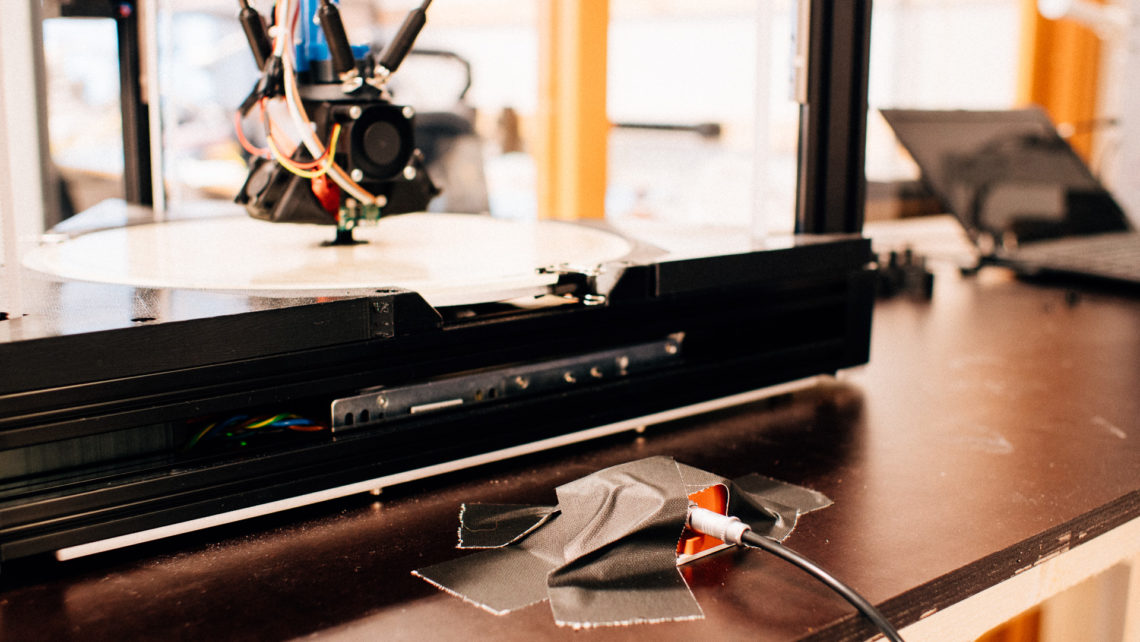
So, we don’t actually have a problem we need to solve. The vibrations from the printer does not affect the print negatively. We’re basically just curious.
Damping
We logged vibrations both without damping and with two forms of damping. For both damping solutions we used this rather soft 8 mm thick rubber mat.
The “Socks”
The first way of damping was to 3D print simple “socks” for the table legs. Inside these socks we put the rubber mats, and underneath the socks we stuck cloth pads to be gentle to the floor.
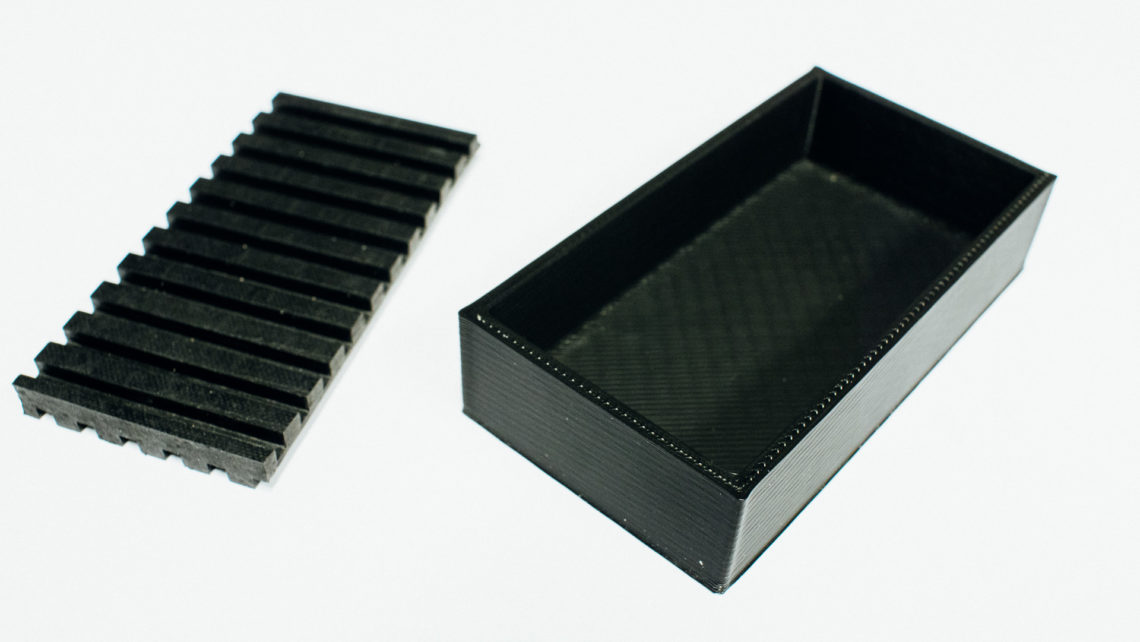
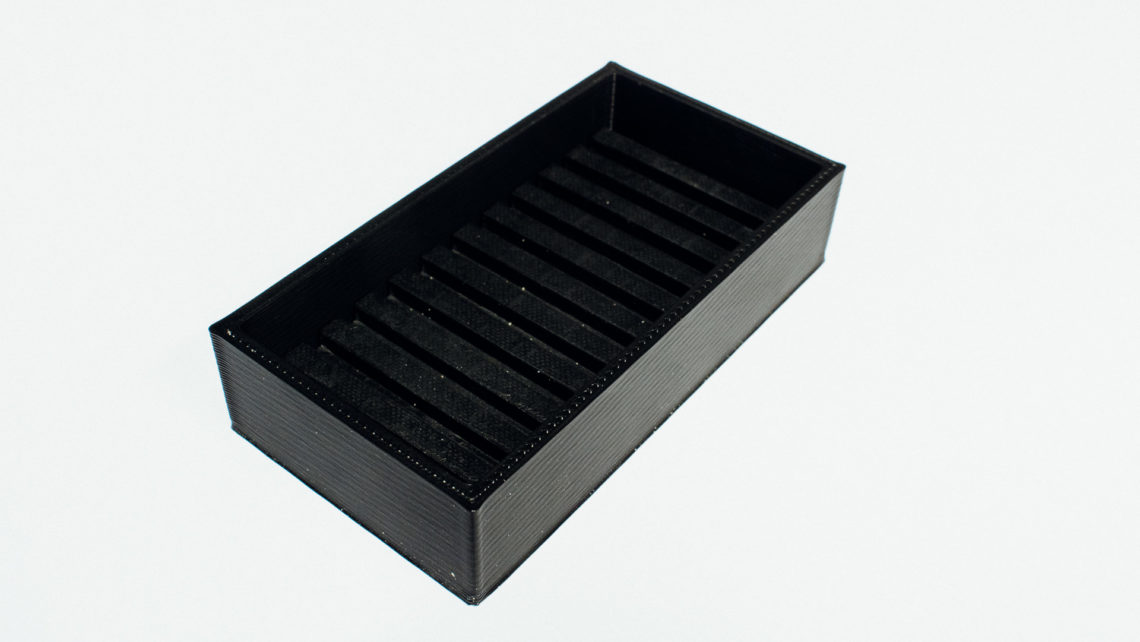
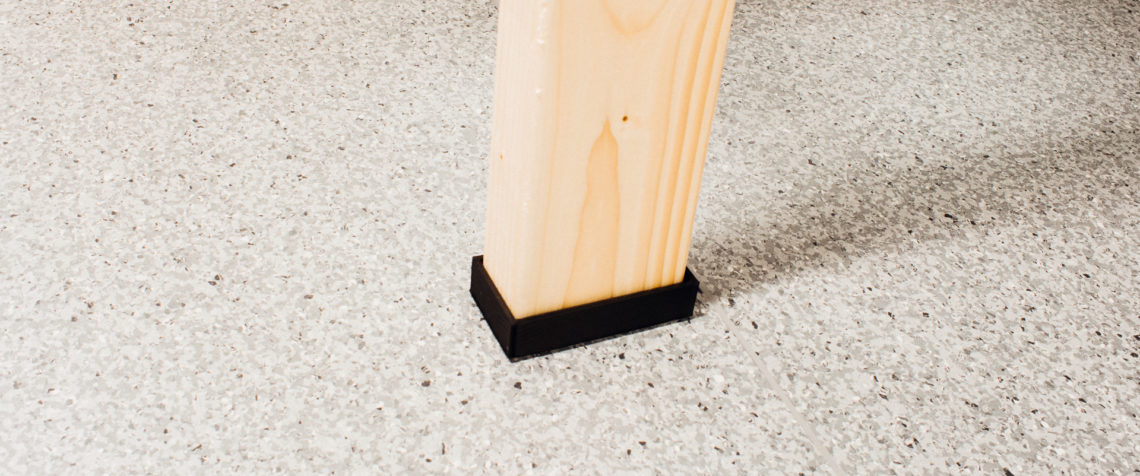
Damping Under the Printer
The other damping method was much simpler where we just put pieces of the same rubber mat directly underneath the printer.
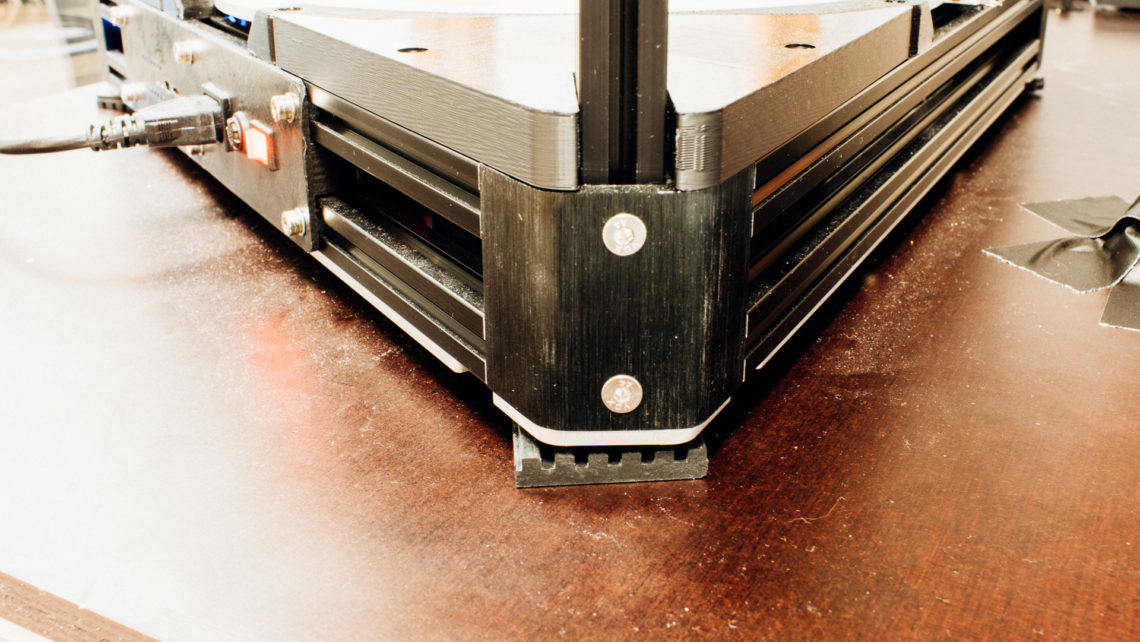
Logging
We attached the AHRS unit to the table and printed a similar piece with the three different damping scenarios. We logged at 2 kHz and only looked at acceleration in the Z-axis (vertical vibrations). Logging and export was easily done with Xsens’ own software.
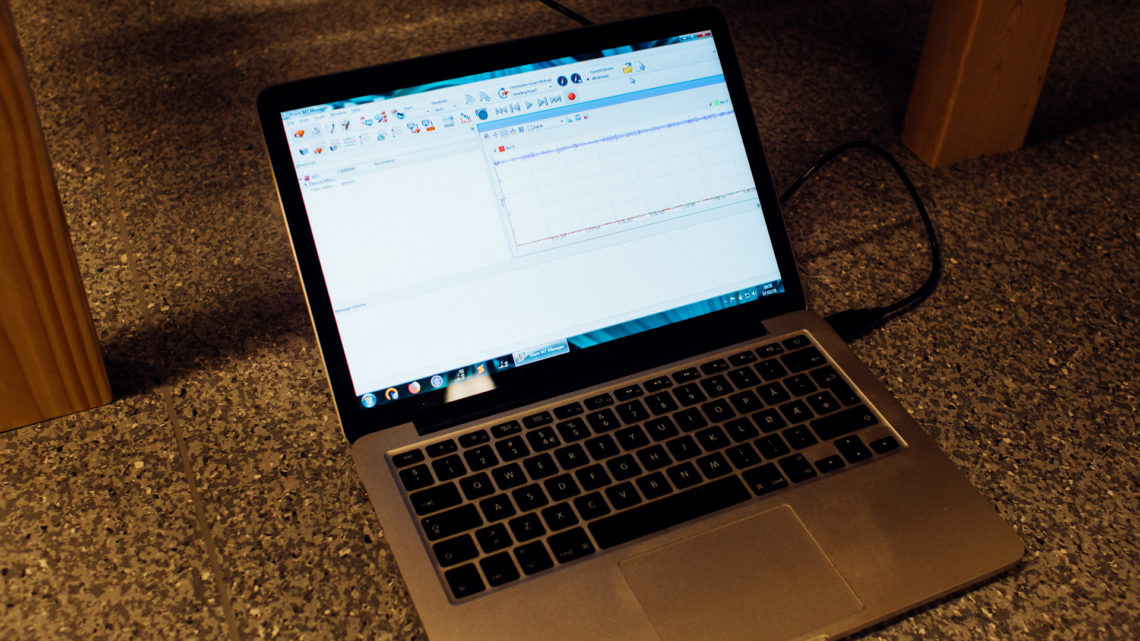
FFT
To make sense of the logged signal we decided to run an FFT analysis on it to see what freqencies were most prominent and what the different damping solutions did to the vibrations. Read more about FFT here.
We used Octave‘s FFT function since MS Excel only supports Fourier analysis over 4096 samples. We had over 630 000.
Visiualization
We brought the analysed into Excel for plotting. We could’ve done this directly in Octave as well.
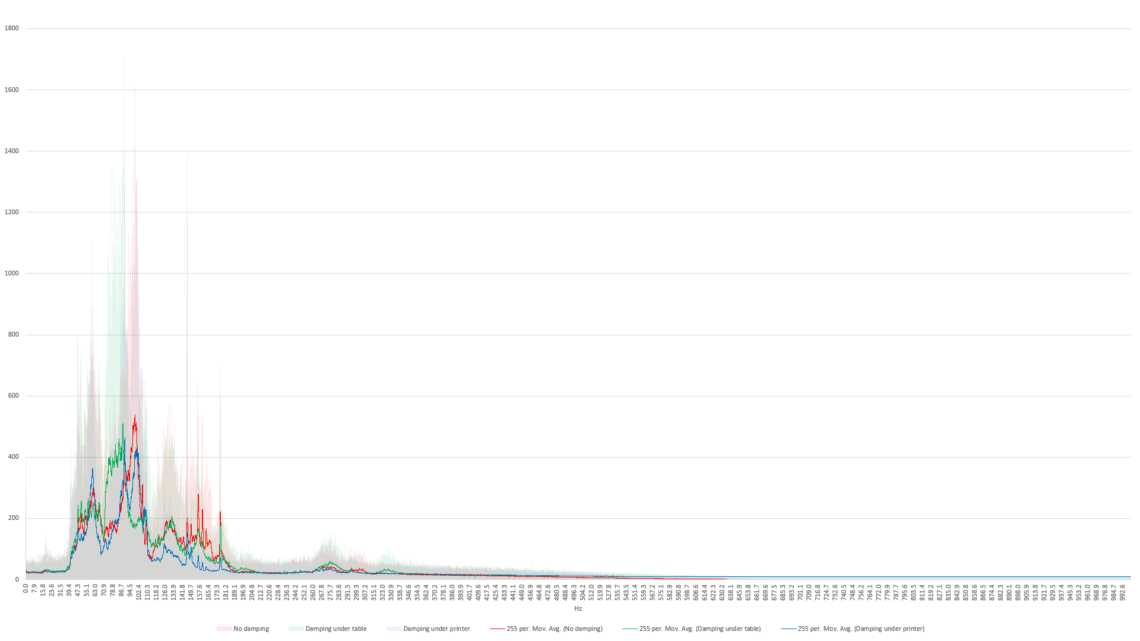
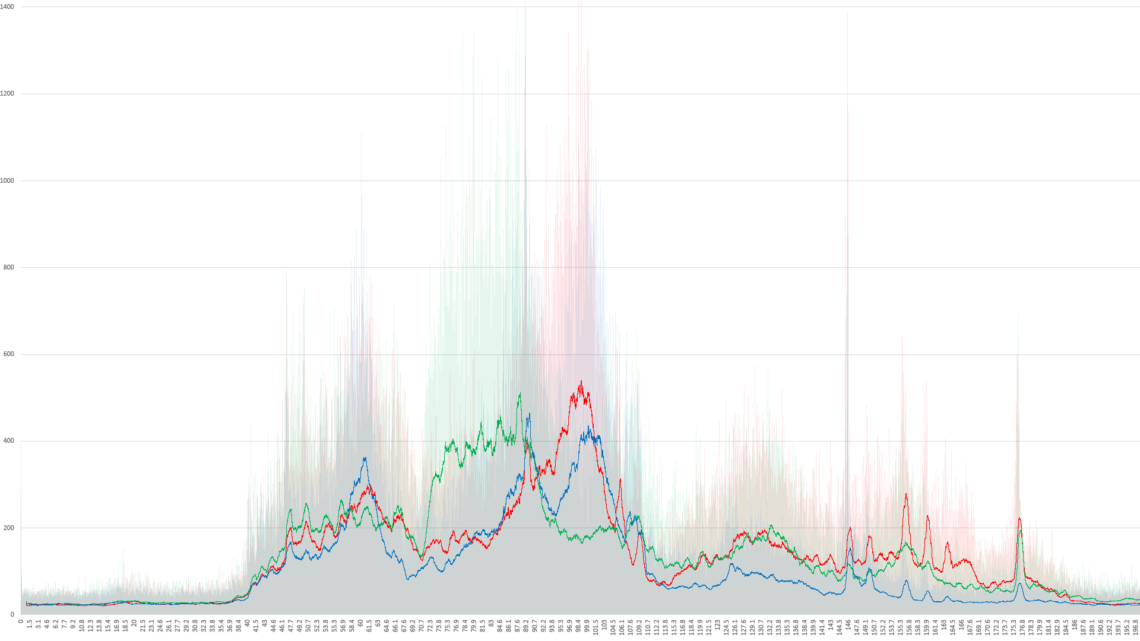
With this many points the raw FFT results aren’t easy to make anything out of. So we’ve kept the raw FFT results somewhat transpartent in the background with a moving average line for each damping case in the front.
Conclusion
From the graph it looks like damping underneath the printer is the way to go if we want to limit the desk vibrations even though the differences aren’t that large. Except for ~60 Hz it is almost always below at least one of the other damping methods. At 70-90 Hz the table damping has issues while at 90-100 Hz the case without damping is the worst. It also has some nasy spikes around 155-165 Hz.